Faster, more accurate receiving and putaway with handheld stock scanners
Reduce errors and improve stock handling with intuitive handheld scanners for receiving, storing, and transferring inventory.
Key features of our Receiving & Putaway technology
Speed up goods handling, improve accuracy, and reduce errors with integrated barcode scanning and smart putaway processes.
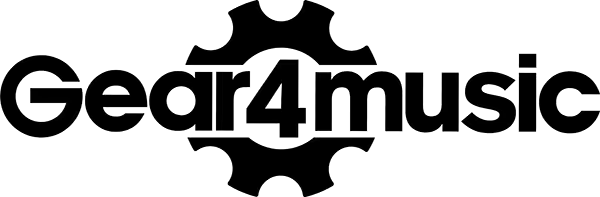
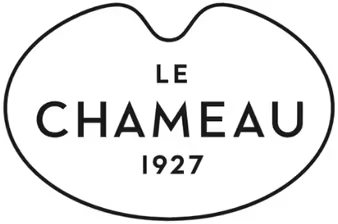
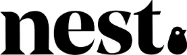
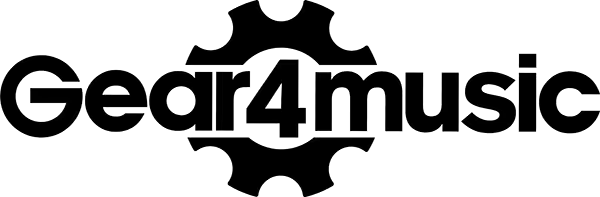
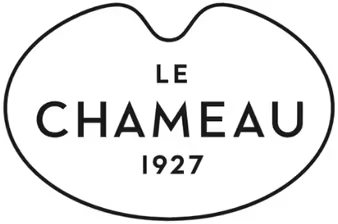
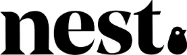
Sell more, manage effectively and drive business growth with Venditan Commerce
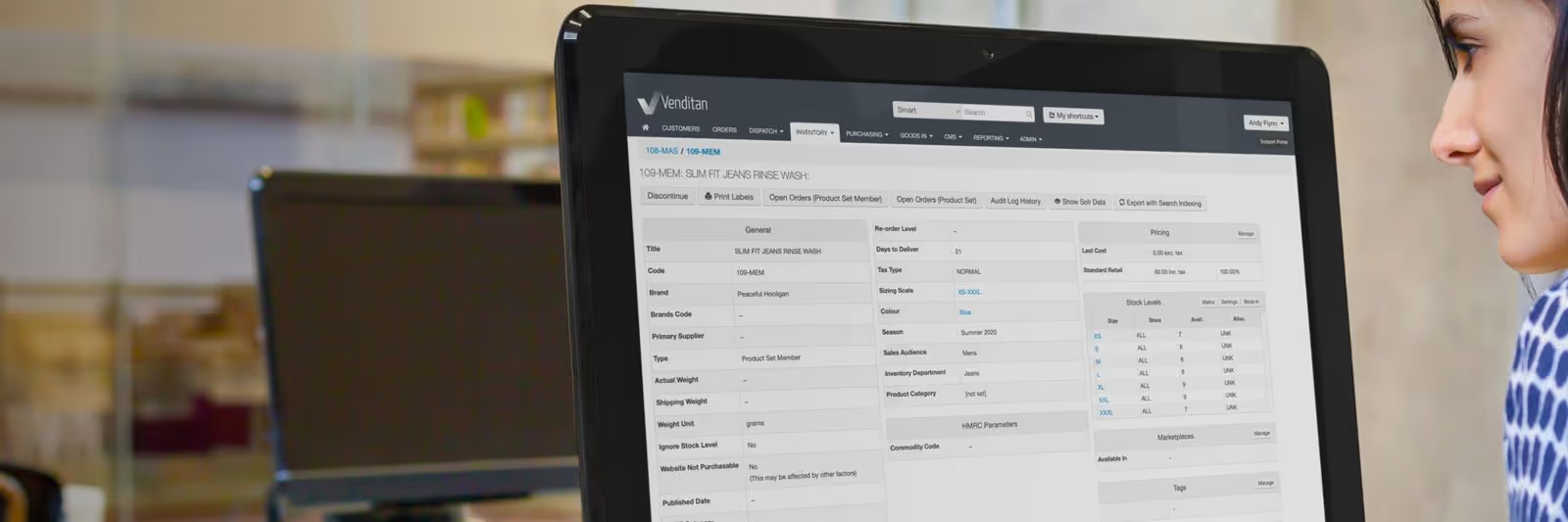
No bottlenecks with quick and efficient inventory booking
We will integrate our eCommerce platform with your suppliers, meaning you can send and automate purchase orders without jumping between systems and emails.
This also means that you will receive advanced shipping notifications (ASN) to the platform, keeping your warehouse team fully aware of any upcoming deliveries and the goods that should be present.
Using our inbound receiving software, they can begin booking in the new stock immediately upon its arrival. The scanners will direct them to the correct storage location based on your pre-determined criteria.
This all means that your team can work rapidly to process new stock into your business, saving countless hours without increasing headcount.
Automatic notifications for discrepancies
When the new stock is processed into your warehouse the pallets can be scanned immediately.
Each item need only be scanned once, and our system will check the following criteria:
- Can an inventory be located for the barcode?
- Does the supplier for the delivery match the supplier for the item?
- Are there any open purchase orders for this item and supplier?
If any of the above checks fail, the handheld will emit an audible warning sound along with a clear message detailing the reason for failure. Once the process is marked as completed on the handheld, a delivery note is logged into your platform for future use.
We have also built a discrepancy management system into this process. Any incomplete orders, such as missing or incorrect items, can be cross-referenced with the original ASN and suppliers can be notified of the mistake.
Work with us to optimise your warehouse strategy
You may wish to work with us on your overarching warehouse strategy as part of your onboarding to our platform.
We work with retailers and distributors who manage their inventory across several warehouses and stores, optimising their inventory management processes and providing them with the technology they need to get more done without increasing their headcount.
Venditan Commerce changes the game
If your existing supplier is no longer keeping up with you, or you’ve outgrown your existing technology, we can help.
Feature-rich and constantly evolving, our platform will solve your growth and efficiency challenges.
Talk to Mike
Discuss your requirements with Mike Smith, Project Lead at Venditan.
Get directions
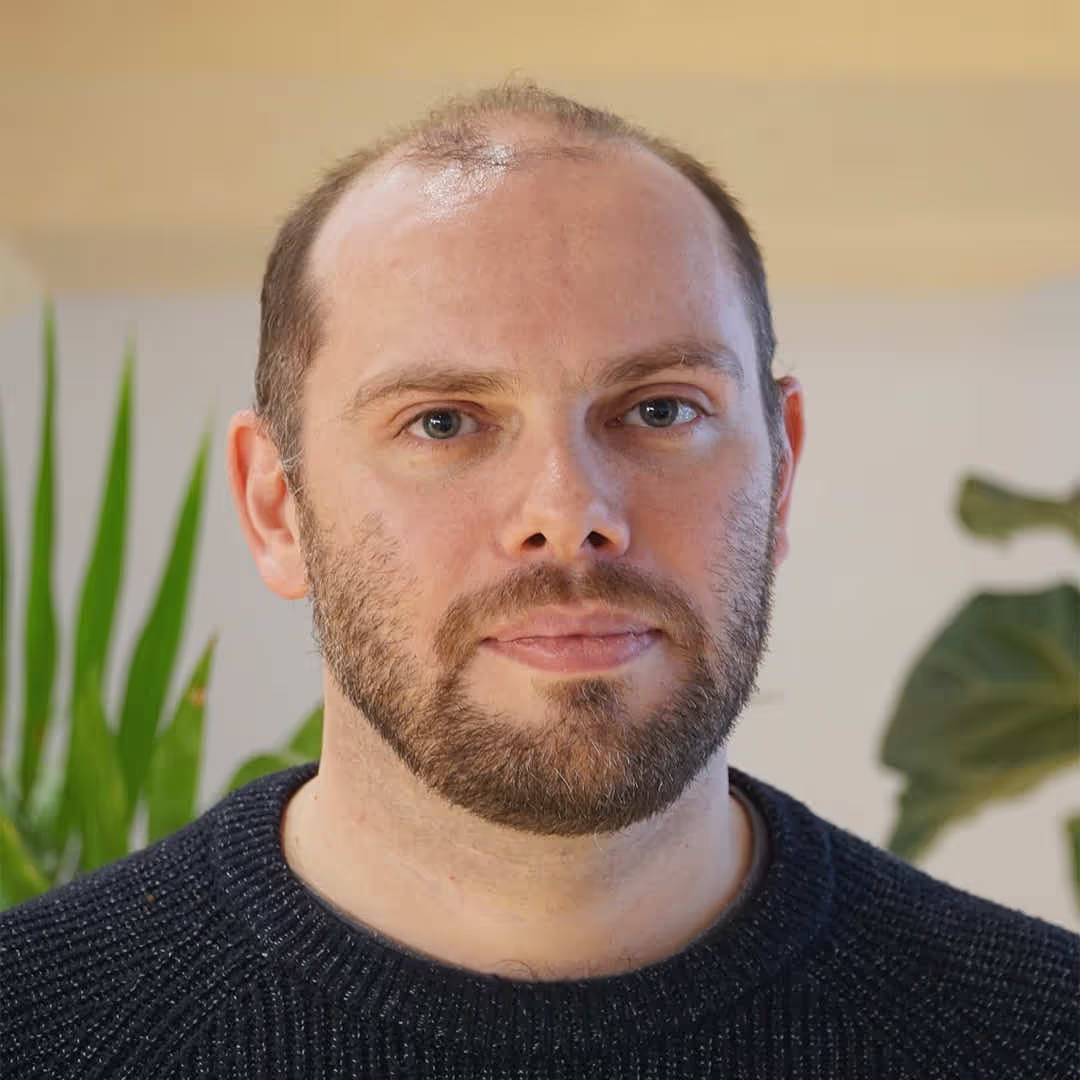