Receiving efficiency and accuracy are vital metrics in warehousing that enable business owners to assess the effectiveness of their receiving processes.
In this article, we will define both metrics and explain how you can calculate them yourself.
Additionally, we will explore several actionable recommendations to help you improve both your receiving efficiency and accuracy.
If you wish to fast-forward to how our technology can help you improve straight out of the box, just click this link: Receiving & Putaway
What is receiving efficiency?
Receiving efficiency demonstrates how effectively you utilise resources and processes to book inventory into your warehouse over a timeframe.
How do you calculate receiving efficiency?
It is measured by establishing three criteria:
- A specified timeframe, such as a working day, week or month.
- The volume of inventory that has passed through the receiving process during the timeframe.
- The number of labour hours utilised by the warehouse during the timeframe.
To calculate receiving efficiency, all you need to do is divide the volume of received inventory by the number of labour hours that were used during the timeframe.
Therefore, the formula for receiving efficiency is:
Volume of Received Inventory ➗ Number of Labour Hours = Receiving Efficiency
Higher numbers are representative of a more efficient business, one that can receive more inventory within the available labour hours.
What is receiving accuracy?
Receiving accuracy is used to measure how accurate you are at correctly booking inventory into your warehouse over a timeframe.
How do you calculate receiving accuracy?
It is measured by establishing three criteria:
- A specified timeframe, such as a working day, week or month.
- The total volume of inventory that has passed through the receiving process during the timeframe.
- The volume of inventory that was correctly put away during the timeframe.
Therefore, the formula for receiving accuracy is:
Volume of Correctly Received Inventory ➗ Volume of Received Inventory = Receiving Accuracy (%)
This figure can be converted into a percentage to give a simple read on how accurate your receiving process is. Of course, the higher the percentage, the better.
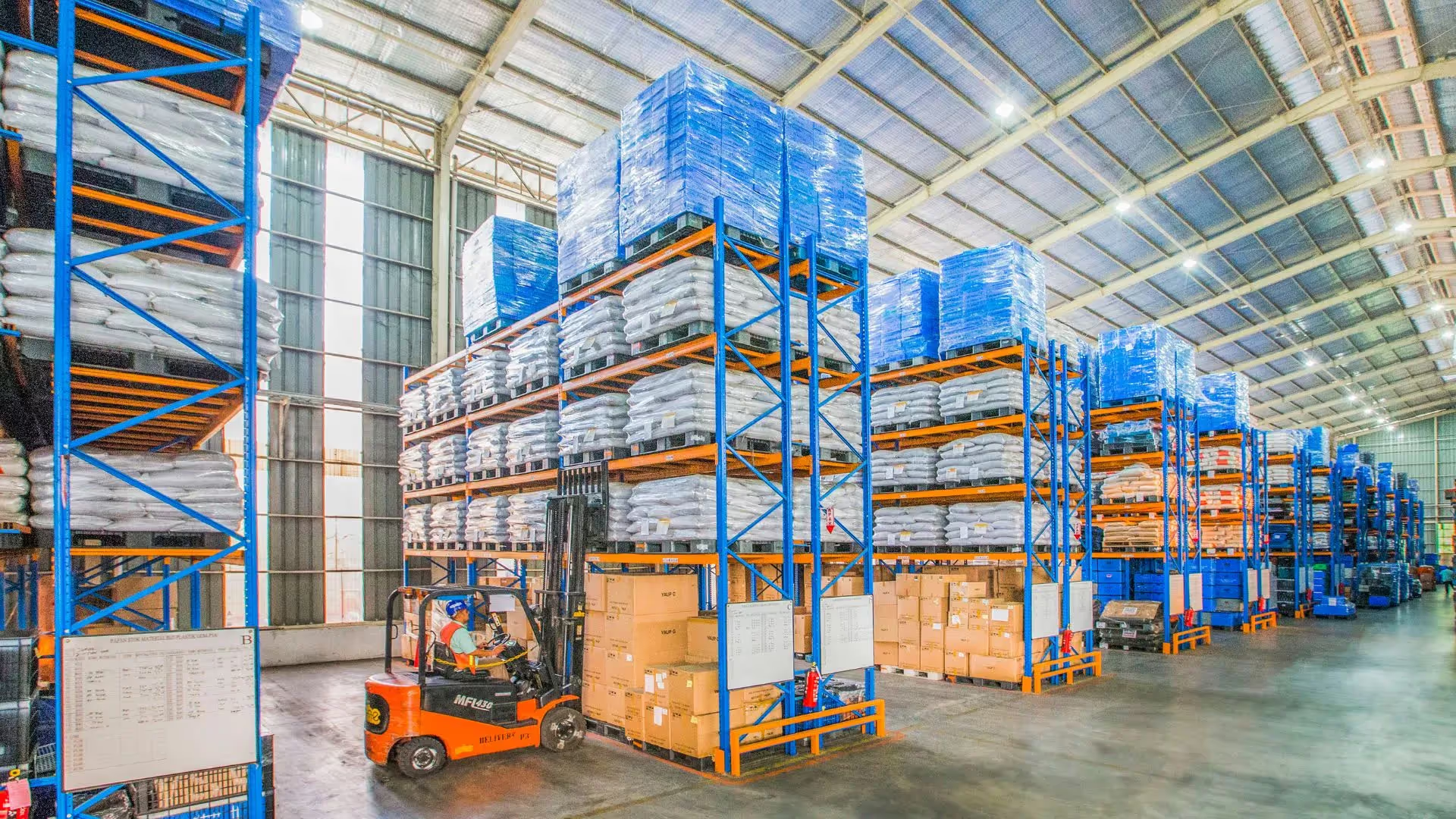
The importance of receiving efficiency and accuracy measurements
Enhancing your warehouse reporting by incorporating measurements of receiving efficiency and accuracy enables you to tangibly monitor your overall receiving performance.
By employing two straightforward KPIs, you can identify drops in performance, prompting a thorough analysis of the root causes. This analysis empowers you to understand the necessary improvements required to maintain a consistently high level of performance.
The faster a warehouse team can log inventory into the business, the sooner it can be made available for sale. Precise inventory logging minimises issues during order picking and dispatch processes, contributing to an efficient business that can achieve more without the need for increased headcount.
Receiving efficiency and accuracy are not one-size-fits-all metrics; they are company-specific and vary significantly across industries. So, establish a baseline measurement and consistently track both KPIs. This approach allows you to monitor and analyse your performance trends over time.
Improving your receiving efficiency and accuracy
Efficient and accurate inventory receiving lays the foundation for streamlined warehouse operations. In this section, we explore five key strategies that businesses can employ to enhance their receiving processes, ensuring optimal efficiency and precision in managing incoming stock.
1. Map out your receiving process flow
Before committing to any significant changes, it can be beneficial to visually map out your current receiving processes. This entails creating a process map, also known as a flowchart or workflow diagram.
Creating a visual representation of the current process helps in gaining a clear understanding of how different elements, such as people, processes, places, and spaces, interact with each other. This clarity is crucial for identifying inefficiencies or areas that need improvement.
A flowchart serves as a communication tool that can be easily shared and understood by various stakeholders. It provides a common visual language that helps in straightforwardly conveying complex processes, acting as a baseline for any future improvements.
2. Review your pre-receiving processes
Pre-receiving constitutes the initial phase of receiving goods before they are officially logged into the inventory system. This stage is critical, playing a crucial role in ensuring the accuracy and integrity of the received inventory.
It can be broken down into several processes, occurring after the physical delivery of goods to the warehouse but before the formal updating of the inventory records.
Communication with suppliers and carriers
Establishing clear communication channels with suppliers and carriers to convey specific protocols and labelling requirements, and obtain essential information, such as the number of items per package, weights, and details about packaging mechanisms.
Streamlining communication leads to reduced lead time in the pre-receiving process. With clear information, the warehouse team can quickly initiate the necessary preparations, inspections, and verifications, accelerating the overall receiving process.
Visual inspection and documentation
Conducting a visual inspection of the incoming inventory to assess its condition and contents. Creating a pre-receiving report that documents the findings of the visual inspection, including any discrepancies or issues observed.
Visual inspection allows warehouse personnel to identify any visible damages to the incoming goods. Detecting damages early on ensures that issues are addressed promptly, preventing the damaged items from being integrated into the inventory and reducing the likelihood of inaccuracies in stock levels.
Verification against Bill of Lading (BOL) or Advanced Shipping Notice (ASN)
Checking and matching the received items against the information provided in the BOL or ASN.
The BOL or ASN typically contains detailed information about the shipped items, including quantities, descriptions, and other relevant details. By cross-referencing this information with the actual received items, warehouse personnel can promptly verify the accuracy of the shipment.
This helps prevent discrepancies and ensures that the right products are received, proactively reducing the chances of errors cascading through the entire receiving process.
On-site communication with the carrier
Promptly informing the carrier of any missing, damaged, or unwanted products. Signing off on the bill of lading only after addressing issues related to damaged or missing goods.
On-site communication with the carrier allows for the immediate resolution of any issues identified during the receiving process. Whether it's damaged goods, missing items, or discrepancies, addressing these issues promptly prevents them from being carried over into the inventory system.
Consistent and effective communication builds a positive relationship between the warehouse and carriers. A strong partnership encourages carriers to uphold high standards in their deliveries, providing the warehouse with accurate and well-handled shipments.
3. Invest in your hardware and software
By investing in a robust Warehouse Management System (WMS), you can achieve a more efficient and accurate warehouse receiving process. This involves leveraging automation, advanced technologies, and integrated systems to increase throughput, reduce errors, and enhance overall operational performance.
Warehouse efficiency with Venditan
We help our clients to receive and put away new inventory efficiently and accurately through the use of our innovative warehouse management software and game-changing eCommerce platform.
Key features include:
Third-party supplier integrations
Our platform can seamlessly integrate with your suppliers, obtaining both product data and stock information. This integration empowers you to gain insights into the current inventory available at your suppliers' warehouses, estimate the lead time for replenishing your stock and raise purchase orders from directly within the system.
Advanced Shipping Notices (ASN)
With these integrations in place, we can pull your ASNs directly into the platform. This pre-notifies receiving teams and keeps them ahead of new shipments.
Handheld devices
Our handheld devices can be used to receive and put away new inventory, as well as for stock taking, movements, replenishment, order picking and remote label printing.
Warehouse staff can promptly begin scanning incoming inventory right from the pallet as it arrives on-site. If multiples of the same item are being received, a single item may be scanned and a quantity selected by tapping on the scanned item.
Discrepancy logging
An audible warning will be triggered if the scanner detects any discrepancies in the received items against the raised purchase order. This is then logged into the platform and can be sent directly back to the supplier.
Goods Received Notes (GRN)
On completion of the delivery, a GRN will be created within the platform, and all scanned inventory will be booked into the system and placed in a default store and bin.
Directed putaway of inventory
Putaway instructions accurately guide the placement of items into designated storage areas, all according to the business’ specific criteria and priorities.
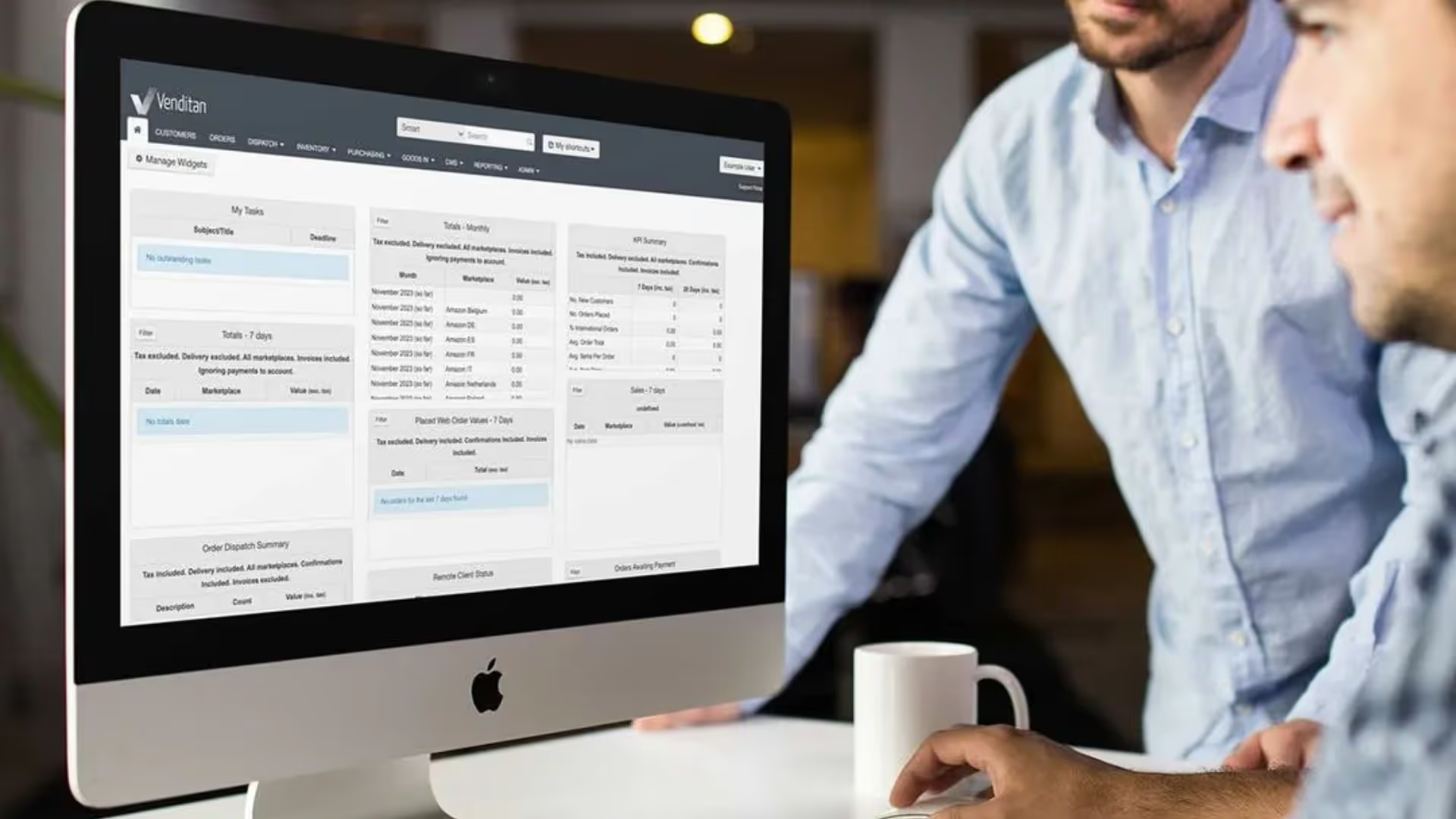
4. Maximise the utilisation of your warehouse space
Optimising warehouse space is crucial for improving the efficiency and accuracy of the inventory-receiving process. While we don’t work directly with our clients on the optimisation of their warehouse space, we do have several pointers based on our experience over the years:
- Design the layout of the dock and warehouse to maximise efficiency. Ensure clear pathways for incoming shipments, segregate areas for different types of products, and create designated spaces for unloading, inspecting, and staging.
- Designate specific areas for pre-receiving and inspecting goods. Streamline the process by ensuring that necessary equipment and tools are readily available. Efficiently designed receiving areas contribute to faster and more accurate inspections.
- Maximise the use of vertical space by installing high shelves or mezzanines. This allows for more storage without expanding the physical footprint of the warehouse. Implementing vertical storage solutions can also facilitate better organisation, accessibility and storage accuracy.
5. Invest in training and create a healthy working environment
Investing in people through training and creating a positive working environment is a strategic investment in the human capital that drives warehouse operations. As employees become more skilled, engaged, and motivated, the entire receiving process benefits from improved efficiency and accuracy.
Training programs provide employees with the skills and knowledge needed to perform their tasks effectively. Well-trained personnel are more likely to understand the intricacies of the receiving process, including proper handling, inspection, and data entry.
Training programs can include communication skills development. Clear and effective communication among team members and with other stakeholders, such as suppliers and carriers, is crucial for preventing misunderstandings and ensuring a smooth receiving process.
If your existing supplier is no longer keeping up with you, or you’ve outgrown your existing technology, we can help.
Feature-rich and constantly evolving, our game-changing eCommerce platform will solve your warehouse efficiency challenges and accelerate your growth.
Our recent posts
Keep up to date with the latest news and insight from the team at Venditan
-p-2000.webp)
.webp)
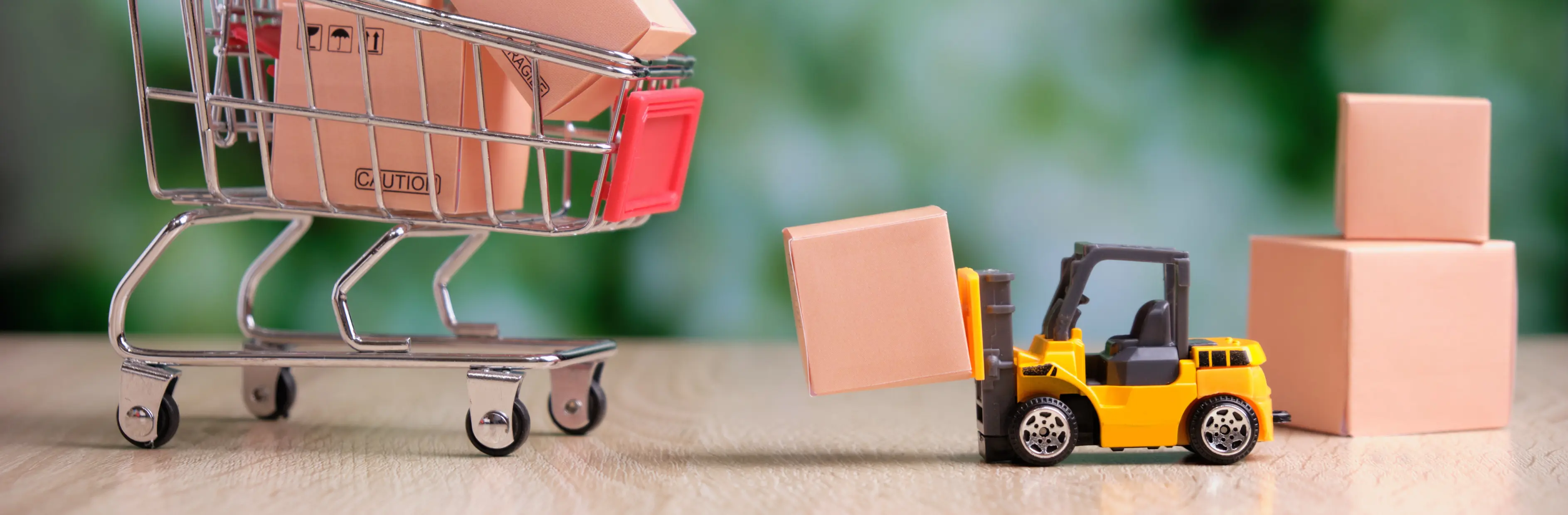
%20(1).webp)
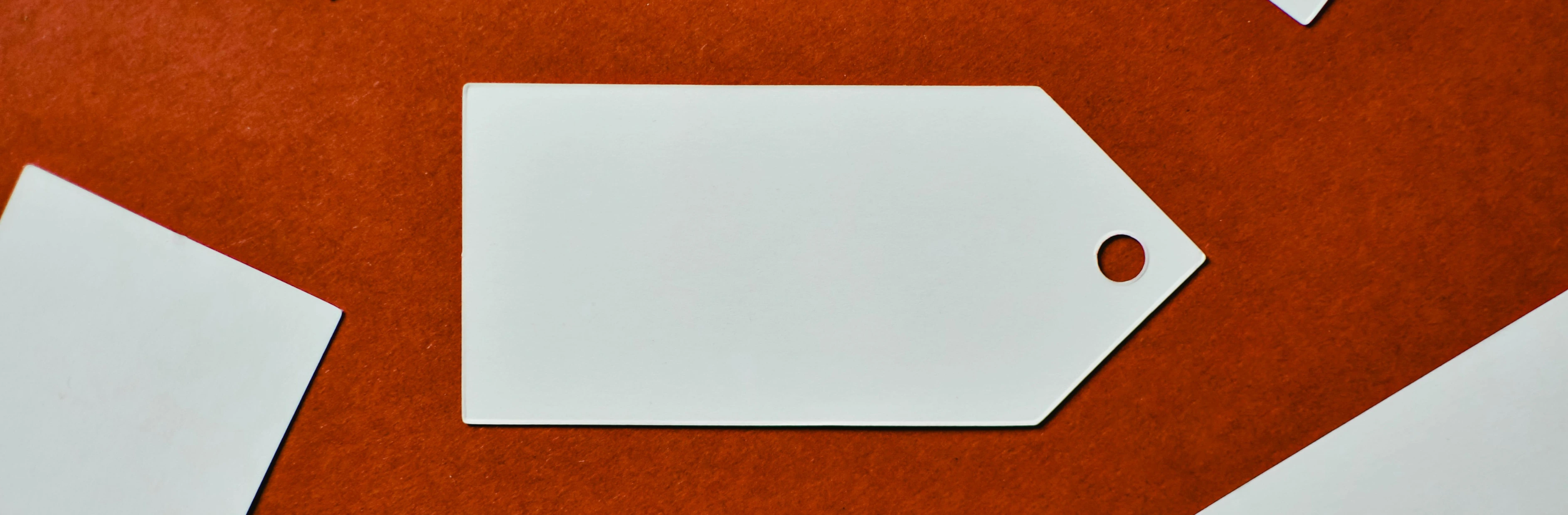